Powder Coating
Powder coating is a unique coating method that involves the application of a dry, free-flowing powder. This versatile technology has seamlessly integrated into various industries, delivering exceptional coating finishes and offering a multitude of benefits in terms of protection and decoration.
Whether metal, wood, or plastic, powder coating can be effectively applied to various materials.
Beyond its decorative capabilities, powder coating provides excellent protection for coated surfaces. The cured powder forms a robust, durable layer that resists chipping, scratching, and fading. This protective barrier shields the underlying material from corrosion, UV radiation, chemicals, and other environmental factors, extending the lifespan of the coated products. Whether applied to automotive parts, industrial machinery, or household items, powder coating ensures long-lasting performance and aesthetics.
We prioritize adherence to international standards in our powder coating process. Our operations strictly follow the guidelines set by BS-6496, and we conduct thorough testing in accordance with BS-3900 par A1 & A3. To ensure optimum quality, we apply a minimum coating thickness of 60-80 microns.
Our expertise lies in providing exceptional metal finishes, which encompass a wide range of options. From polyester powder coating to epoxy polyester and super durables, we offer a diverse selection of finishes to meet the unique requirements of our clients.
By upholding international standards and offering a variety of high-quality metal finishes, we strive to deliver excellence and customer satisfaction with every project we undertake. Trust Standard Metal Contracting for superior powder coating solutions that meet the highest industry standards.





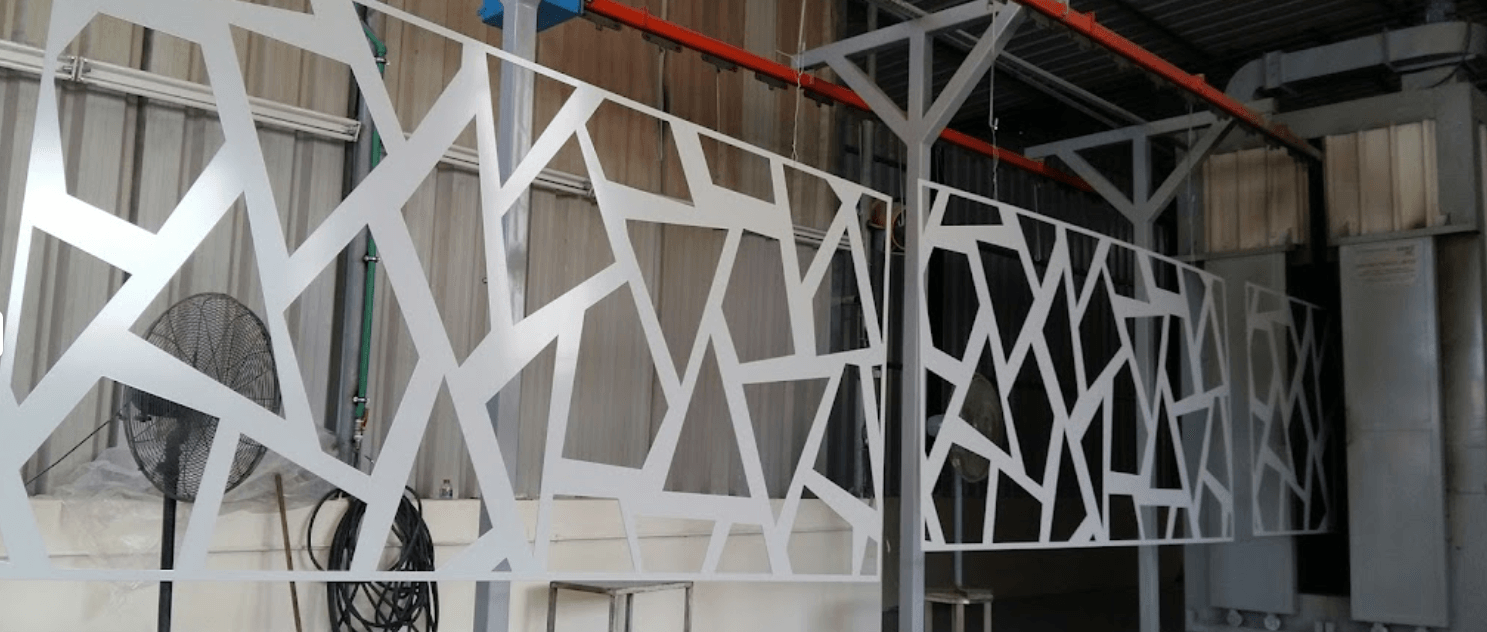
Powder Coating Durability:
- Enhanced Finish Durability: Powder coating surpasses the durability of liquid coatings, offering a finish that can withstand the test of time while maintaining its attractive appearance.
- Resistance to Various Elements: Materials that are powder coated exhibit exceptional resistance to impact, ultraviolet light, chemicals, moisture, and extreme weather conditions. This resilience ensures that the coating quality remains unaffected by these external factors.
- Reduced Wear and Tear: Powder coating significantly lowers the risk of scratches, chipping, abrasions, corrosion, fading, and other wear issues commonly affecting surfaces. The robust coating acts as a protective barrier, preserving the integrity and aesthetics of the coated materials.
- Environmentally Friendly: Unlike liquid paint, powder coating is solvent-free, which makes it environmentally friendly and reduces the emission of volatile organic compounds (VOCs). The process produces minimal waste as any overspray can be collected and reused, minimizing material waste and lowering production costs.
Electrostatic Powder Coating: Environmentally Friendly and Superior Coating Method
To facilitate this process, powder coating operations are carried out within a specialized enclosure known as a powder booth. Any un-deposited thermosetting powder is safely vented out of the booth, and the coated workpiece undergoes curing in an oven.
Our innovative powder coating company prioritizes meeting our customers’ quality, delivery, and satisfaction requirements. Our production facilities are equipped with the latest technology machinery, operated by our skilled staff, ensuring exceptional results. We take pride in providing suitable guarantees and warranty periods for the goods we coat, giving our customers peace of mind and confidence in the durability and performance of our finishes.

Galvanizing
Benefits of Proper Venting and Draining in Galvanised Coating:
Complete Protection: With appropriate venting and draining design, the molten zinc used in the galvanizing process covers corners, welds, seals edges, and penetrates recesses, ensuring comprehensive protection for areas prone to corrosion. This provides superior coverage compared to other coating systems.
Thicker Coating at Critical Areas: The galvanized coating is slightly wider at corners and narrow edges, offering enhanced protection. This is particularly beneficial as these areas are often vulnerable to damage and corrosion. In contrast, organic coatings tend to thin out in these critical spots.
Suitable for Complex Shapes: Galvanizing allows for coating complex shapes and open vessels inside and out in a single operation. This ensures uniform protection for intricate structures, eliminating the need for multiple coating processes.
Varying Immersion Period: The immersion time in the galvanizing bath varies depending on the weight and size of the articles being galvanized. Lighter items may require only a few minutes, while heavier structural members may require a more extended immersion period to ensure complete coverage and protection.
Controlled Cooling Process: After extraction from the galvanizing bath, the galvanized article is typically cooled using a quench solution. This solution often contains an inhibitor that passivates the zinc surface, preventing early oxidation and ensuring long-lasting protection.
By incorporating proper venting and draining techniques, galvanized coatings provide comprehensive coverage, thicker protection at critical areas, and the ability to coat complex shapes. The process is flexible, adapting to the needs of different articles, and concludes with controlled cooling to maintain the coating’s integrity. Choose galvanized coatings for reliable, long-lasting corrosion protection.
Sand Blasting
A sandblasting system comprises four essential components: the air source, the sandblasting cabinet, the dust collector, and the blasting media. The air source is typically provided by bottled gas or an air compressor. Within the sandblasting cabinet, the object being blasted is securely held while the dust collector efficiently removes dust particles from the cabinet. The materials employed in sandblasting, whether actual sand is used or not, are known as blast media.
Sandblasting is a fast and efficient method for removing various materials’ powder coats, rust, and oxidation residue. It can also be utilized to alter the surface condition of metals by eliminating scratches or casting marks. With a history spanning over a century, sandblasting has established itself as a widely employed cleaning technique.
FINAL INSPECTION
Our team of highly skilled QA/QC engineers meticulously assesses and approves the quality of our products before they are carefully packed and dispatched.


FAQs:
Powder coating is a dry finishing process where a fine powder is electrostatically applied to a surface and then cured under heat to create a durable and protective coating.
Powder coating offers several advantages, including superior durability, resistance to chipping, scratching, and fading, enhanced aesthetics, environmental friendliness (no solvents or VOC emissions), and the ability to coat complex shapes evenly.
Powder coating is suitable for a wide range of materials, including metals like steel, aluminum, and iron, as well as some non-metal materials such as plastics and MDF (Medium-Density Fiberboard).
With proper application and maintenance, powder coating can last for many years. The longevity of the coating depends on factors like the quality of the coating, exposure to environmental conditions, and the level of care given to the coated surface.
In most cases, yes. However, proper surface preparation is crucial to ensure adhesion and durability. Existing coatings should be thoroughly cleaned and properly prepped before applying a new powder coating.
Yes, powder coating provides excellent resistance to corrosion. The coating acts as a protective barrier, shielding the underlying surface from moisture, chemicals, and other corrosive elements.
Absolutely. Powder coating offers a wide range of colors, textures, and finishes to choose from. Custom colors can be achieved through color matching services, allowing you to achieve your desired aesthetic for your project.
The time required for powder coating varies depending on factors such as the size and complexity of the item being coated, the color and finish selected, and the current workload of the coating facility. Typically, the process can take a few days to a couple of weeks.
Powder coated surfaces can be cleaned with mild soap and water using a soft cloth or sponge. Avoid abrasive cleaners or tools that could scratch the coating. Regular maintenance and cleaning will help preserve the appearance and longevity of the powder coating.
Yes, powder coating can be repaired. Minor damages such as chips or scratches can be touched up using specialized repair kits or by a professional powder coating service provider.